Two-Stage MBR Plant | One of its kind wastewater treatment plant in India
Detox Corporation Private Limited part of the Veolia Group company is working in the environment and infrastructure sector for the last thirty years. The firm is ISO 9001: 2008 Certified and the laboratory is certified OSHAS 18001: 2007. Detox is located at Ankleshwar Industrial Park popularly known as Ankleshwar GIDC. Ankleshwar is one of the most prominent MSME chemical clusters in the country. The cluster in Ankleshwar is spread over an area of 1,600 hectares and has proximity to the National Highway 8 (NH 8) and Delhi–Mumbai Railway Line. The setting up of large industries like UPL, Atul, Rallis India, Glaxo, Pfizer, Sterlite, Cadila, and Sun Pharma in this region provided a major boost to rapid industrialization in the cluster. Chemical industries in Ankleshwar manufacture a diverse range of products like dyes and dye intermediates, pigments, pesticides/insecticides, petrochemicals, agrochemicals, Chlor-alkali, pharmaceuticals, paints, and so on.
Today, the chemical industries of Ankleshwar face several challenges specially to control their effluent discharge and pollution. The effluent generated from these industries contains very complex organic and inorganic contamination which is very difficult to treat as per the norms. Given that there are numerous chemical industries in the region and effluent from all these industries are fed to the Common Effluent Treatment Plant (CETP) for treatment. The complexity and variety in the effluent characteristics were a major issue for all the companies who were bidding for this project.
Major challenges
• Complexity and varied effluent nature
• High COD – 4696 (3896 – Biodegradable, 800 – Non-Biodegradable)
• High Temperature
Typical to a chemical industry that too in a common effluent treatment plant, the major challenge was diverse and wide range of chemicals produced by different industries, consisting of more complex molecules with different bio degradability levels, presence of refractory organics and inorganic compounds and also periodic change in effluent characteristics. This required a more robust and more reliable system which can meet these difficult challenges and deliver a consistent treated water quality to make recycling through Reverse Osmosis possible.
Detox initiated the discussion with Arvind Envisol a well-known EPC company in the water industry. Arvind Envisol a wastewater arm of the textile conglomerate Arvind Limited has expertise in treating such challenging effluent. The PFET technology sold by Envisol is one of the best ZLD technologies available in India. Arvind Envisol did numerous discussions evaluating different technologies for this project. Finally, both the companies mutually agreed to use Membrane Bio-Reactor (MBR) in this ETP plant. However, there was a bigger challenge waiting for them. The harsh quality of effluent and the nature of uncertainty will have a larger impact on the life of membranes. There was a possibility of membranes getting fouled after a few months. To cope with this issue, the technical team of Arvind Envisol has proposed to set up a two-stage MBR plant to treat this uncertain effluent. No other company in India has set up a two-stage MBR plant. There are two type of MBR available in the market TIPS and NIPS. Arvind Envisol has used MBR manufactured using TIPS technology. TIPS MBR provides higher resistance to chemicals and are very durable. A detailed comparison between TIPS and NIPS is shown below.
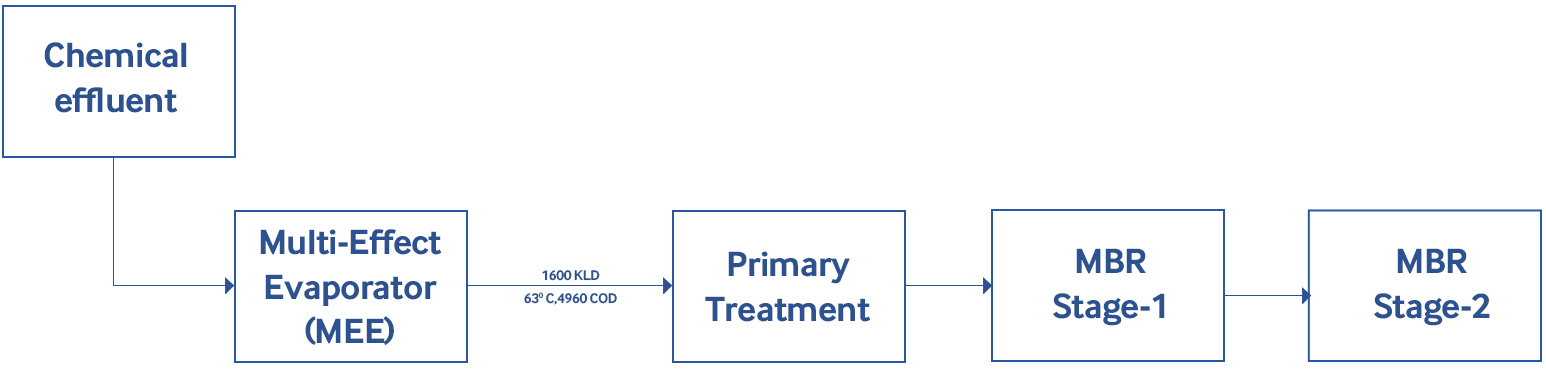
Effluent Characteristics
Sr. No | Constituents | Unit | Inlet Parameters | Outlet Parameters |
---|---|---|---|---|
1 | Flow | KLD | 1620 | 1602 |
2 | pH | 9 | 7.5-8.5 | |
3 | COD | ppm | 4696 | < 850 (considering 800 ppm non-biodegradable COD) |
4 | BOD | ppm | 3275 | <10 |
5 | AN (Ammonical Nitrogen) | ppm | 296.5 | <30 |
6 | TSS | ppm | 50 | <=5 |
7 | Oil & Grease | ppm | NIL | NIL |
8 | TDS | ppm | 506 | 506 |
9 | Temperature | Degree C | <63 | <32 |
10 | Sulphite | ppm | <150 | <10 |
Benefits of TIPS MBR
Factors | Arvind Envisol | Competition |
---|---|---|
Type | 3G TIPS (Thermal Induced Phase Separation) | Supported NIPS (Non-Solvent Induced Phase Separation) |
MOC | PVDF | PVDF |
Wear & Tear | No wear & tear as full PVDF | High chances of pilling top PVDF thin layer |
Chemical Resistance | High | Low |
Ph Range | 1-12 | 2-10.5 |
Max Chlorine Tolerance | 1000000 ppm-hrs | 500000 ppm-hrs |
Max allowed Chlorine | 5000 ppm | 1000 - 2000 ppm |
Mechanical Strength | High | Low |
Vertical Length | 1.2 Meter | 2.2 Meter |
Staking | Multiple stacking possible-Double Decker Skid Design Possible | Not Possible |
Temp withstanding capacity | High at 45 Deg C max. | Low at 40 Deg C max. |