MBR is one of the important methods of secondary treatment of wastewater. Secondary treatment is used to treat the wastewater by reducing reduce BOD and COD of effluent and removing the settleable solids using phase separation process. Secondary treatment is usually performed by indigenous, aquatic microorganisms in an aerobic environment. Bacteria and protozoa’s consume biodegradable soluble organic contaminants. This performance of this treatment process is highly dependent on temperature. Fluctuations in temperature may affect the growth of microorganisms in the effluent.
There are several processes that can be used to treat effluent in secondary treatment.
- Activated Sludge Process (ASP)
- Extended Aeration System (EAS)
- Membrane Bio-Reactor (MBR)
- Moving Bed Biofilm Reactor (MBBR)
- Sequential Batch Reactor (SBR)
- Up-flow Anaerobic Sludge Bioreactor (UASB)
Membrane Bio-Reactor (MBR)
- Membrane Bio-Reactors provide the benefits of biological treatment with a physical barrier separation.
- Unlike other conventional secondary treatment processes, MBR uses membrane modules to treat the water. The high quality of effluent generated can be discharged directly to surface water for reuse.
- The efficiency of this system depends upon the scheme and its configuration selected.
- Installing an MBR plant replaces the need forsecondary clarifier, filtration process and Ultra-filtration. However, it has an implication on the capital investment and the operating cost of the plant.
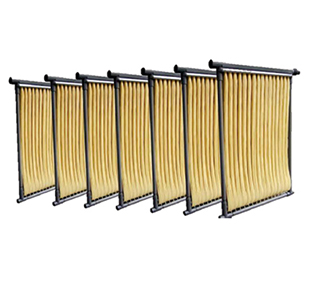
MBR Process
In this process, below listed things are used.
- Equalization tank / Feed tank
- In some industries, effluent from multiple streams is fed into the process. The characteristics of the effluent will not be the same every time. To bring the parameters of the effluent at equilibrium a tank is needed. Equalization tanks are used to reduce the amount of chemicals utilized, minimize temperature variations, maintain the appropriate PH level, reduce the impact of inhibiting constituents, balance levels of organic composites, and equalize the rate of movement.
- Rotary screen
- A rotary screen is used to remove the suspended solids of size 1 – 2 mm present in the effluent. These solids can foul the MBR membranes when not retained earlier.
- Aeration tank
- Mixed liquor suspended solids (MLSS) are developed in the aeration tank. MLSS ensures that there is enough amount of biomass to consume organic pollutants (BOD and COD) present in the effluent. It is an aerobic process. Hence, an optimum level of Dissolved Oxygen (DO) has to be maintained so as to increase the growth of microorganisms.
- MBR tank
-
- The water with required MLSS enters the MBR tank after aeration. MBR tank consists ofthe membrane modules mounted on a structural frame along with the back pulse tank arrangement on the top.
- The Compact tubular membrane is very well suited for the separation of biological sludge or any other high solids application in which high effluent quality is required.
- Separating the suspended solids before the bioreactor, this membrane filter allows only water and dissolved matter to pass, rejecting everything that is undissolved.
- Permeate and reject tank
- The filtrate can either be used directly in many applications or can be fed into another (RO) treatment system to remove the dissolved matter.
-
Configuration of MBR
There are two main configurations available in the market.
- Submerged
- This filtration system is installed in the main bioreactor vessel or in a separate tank.
- It reduces the footprint of the system.
- Side-stream
- This filtration system is installed in outside the bioreactor vessel.
- This system is most commonly used because at the time of maintenance a part of the system can be shut down without stopping the treatment completely.
However, the design of the system is dependent on the design considerations and individual project.
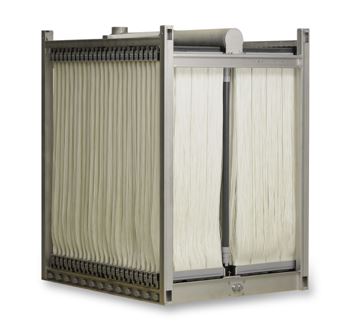
Advantages of this system
- The development of MBR system has reduced the footprint required thus by eliminating the need for large clarification basins
- In the conventional system, good quality of effluent is dependent on the settling characteristics of biomass. MBR prevents the loss of biomass.
- Conventional systems are limited to the solid concentration of 5mg/l while the MBR process can handle solid concentrations of up to 25 mg/l that allows a larger retention time and a reduced footprint requirement
- The MBR plant’s capacity can be increased easily by increasing the MBR modules if the organic loading increases in the future. It does not need the creation of any additional tank which is required in the case of the conventional treatment process.
- MBR system gives 100% removal of suspended solids. It can handle the effluent that has BOD and COD load rate of 6,500 mg/l and 13,500 mg/l respectively. Removal of COD is guaranteed in the range of 89% to 97%.
- In the MBR system as the biomass generation is less, it develops a low amount of sludge compared to the conventional system.
- It is highly tolerant to hypochlorite cleaning.
Quality of effluent at the outlet of the MBR process
BOD | <5 | mg/l |
COD | <30 | mg/l |
NH3 | <1 | mg/l |
Total N | <10 | mg/l |
Turbidity | <1 | NTU |
P* | <0.5 | mg/l |
We at Arvind Envisol have the technical expertise to install this technology at your industry. A team of water industry experts guide us to select, design and install this system. We have another entity called “KaiGO” that deals into the manufacturing and sales of the components that we use to install the system.
To learn more about MBR or get a free consultation for you wastewater treatment requirements, contact us today by clicking here.