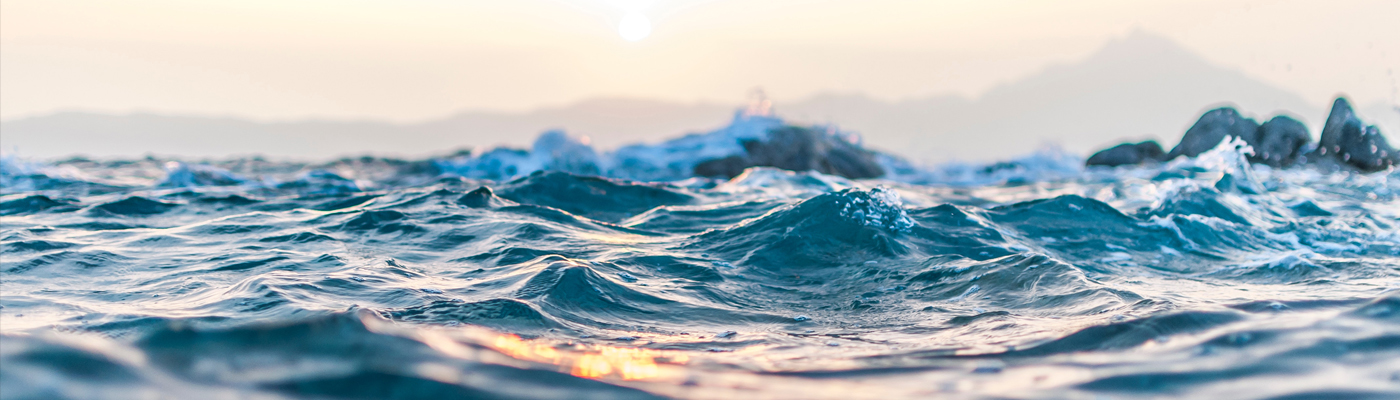
Industries
Arvind Envisol has proprietary technologies for cost-effective water treatment which includes recycling and recovering. Our water
conservation solutions are used across the globe for industrial, commercial, and municipal applications. Water
optimisation is a critical component of modern establishments given the urgent need to save and recover water. We have the
technologies linked with the know-how and experience to provide customised wastewater treatment solutions.
TEXTILE INDUSTRY
Textiles, one of the major industries in the world consists of numerous processes like spinning, weaving, dyeing, singeing, and scouring. The dyeing process is explicitly water intensive, roughly about 200L of water is used to produce 1 kg of textile.
Depending on the type of fiber used-cellulose, protein or synthetic, various kinds of dyes are consumed. They include reactive, direct naphthol, indigo, acid, lanaset, disperse dyes etc. Thus, the key challenge in setting up a treatment process is to be able to handle all these different dyes. Besides dyes, the wastewater produced also contains trace metals such as Cr, As, Cu and Zn which are capable of harming the environment and human health.
If left incorrectly treated, The textile wastewater can cause haemorrhage, ulceration of skin, nausea, skin irritation, and dermatitis. The chemicals present in the water block the sunlight and increases the biological oxygen demand, thereby inhibiting photosynthesis and re-oxygenation process.
The effluent water discharged from the textile industries undergoes various physio-chemical processes such as flocculation, and coagulation followed by biological treatments for the removal of nitrogen, organics, phosphorous, and metal. The whole treatment process involves three steps:-
1. Primary Treatment/Physio-chemical Treatment
- The primary treatment involves removal of suspended solids, oil, grease, and granular materials
- Recommended process: Dissolved Air Flotation (DAF)
2. Secondary Treatment/Biological Treatment
- The secondary treatment is carried out by micro-organisms under aerobic or anaerobic conditions and involves the reduction of BOD, COD, and nutrients present in the water
- Recommended process: Membrane Bioreactor (MBR)
3. Tertiary Treatment
- The tertiary treatment involves the use of filtration process, Ultrafiltration (UF), Reverse Osmosis (RO), and ion exchange for removing the final contaminants in the wastewater
- Recommended process: Reverse Osmosis (RO)
4. Zero Liquid Discharge
- Evaporator (PFET) and Crystallizer (MEE) are used further to treat the reject of tertiary treatment.
- Recommended process: Polymeric Film Evaporation Technology (PFET) at the end of all these processes we are able to get approximately 90% of pure water from the effluent fed. With our vast experience and installed base in the textile industry and a thorough knowledge of its various manufacturing processes and also its requirement for uninterrupted water supply
Process | Water Consumption (L/1000 kg of products) |
---|---|
Sizing | 500-8200 |
Desizing | 2500-21000 |
Scouring | 20000-45000 |
Bleaching | 2500-25000 |
Mercerizing | 17000-32000 |
Dyeing | 10000-300000 |
Printing | 8000-16000 |
Source of effluent generation | Parameters | ||
---|---|---|---|
pH | COD(mg/L) | BOD(mg/L) | |
Process Effluent | |||
Desizing | 5.83-6.50 | 10000-15000 | 1700-5200 |
Scouring | 10-13 | 1200-3300 | 260-400 |
Bleaching | 8.5-9.6 | 150-500 | 50-100 |
Mercerizing | 8-10 | 100-200 | 20-50 |
Dyeing | 7-10 | 1000-3000 | 400-1200 |
Wash Effluent | |||
After Beaching | 8-9 | 50-100 | 10-20 |
After Acid Rinsing | 6.5-7.6 | 120-250 | 25-50 |
After Dyeing (Hot Wash) | 7.5-8.5 | 300-500 | 100-200 |
After Dyeing (Acid & Soap Wash) | 7.5-8.64 | 50-100 | 25-50 |
After Dyeing (Final Wash) | 7-7.8 | 25-50 | |
Printing Washing | 8-9 | 250-450 | 115-150 |
Blanket Washing of Rotary Printer | 7-8 | 100-150 | 25-50 |