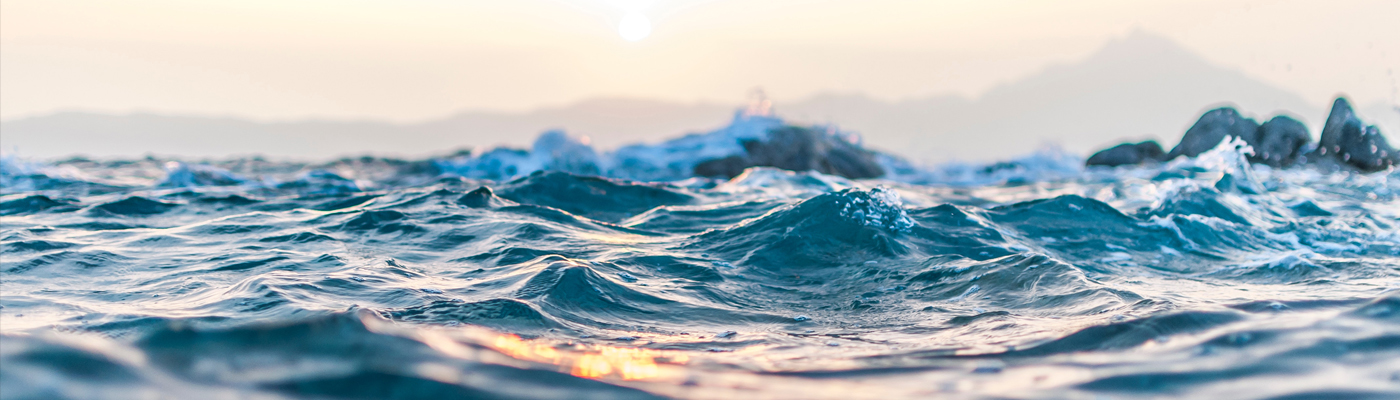
Solutions
Arvind Envisol is a world-class water management company providing end to end solutions for water treatment, industrial wastewater treatment, sewage treatment, desalination and Zero Liquid Discharge (ZLD) solutions at minimal costs. We have experience in designing and treating hard to treat effluent at a very nominal cost. Our expertise lies in bringing our teams together for the seamless implementation of the project. We work to implicate new technologies, reduce footprint, save energy, and deliver a state of the art water treatment plant.
- Effluent Treatment Plant (ETP)
- Sewage Treatment Plant (STP)
- Packaged Sewage Treatment Plant (PSTP)
- Zero Liquid Discharge (ZLD)
- Solid Waste Treatment (SWT)
EFFLUENT TREATMENT PLANT (ETP) MANUFACTURERS IN INDIA
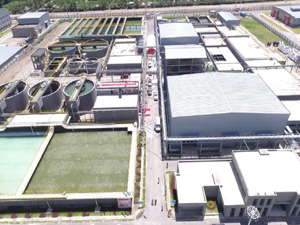
Effluent is generated in many manufacturing industries like textile, pharmaceuticals and chemicals, tanneries etc. Contaminated water cannot be released without treatment as it contains toxic and non-toxic chemicals. Releasing it may cause contamination of the existing pure water and will affect the environment. As a result ETP’s are installed in most manufacturing industries.
The Effluent treatment plants (ETP) are used for the removal of high amounts of organic compounds, debris, dirt, grit, pollution, toxic, non-toxic materials and polymers etc. from industrial effluent. The ETP plants use evaporation and drying methods and other auxiliary techniques such as centrifuging, filtration , incineration for chemical processing and effluent treatment.
ETP Plant Operation
1. Screen Chamber:-
- This chamber removes relatively large solid to avoid abrasion of mechanical equipment and clogging of hydraulic system.
2. Collection Tank:-
- The collection tank collects the effluent water from the screening chamber, stores and then pumps it to the equalization tank.
3. Equalization Tank:-
- The effluents do not have similar concentration at all the time; the pH will vary time to time.
- Effluents are stored for up to 8 to 12 hours in an equalization tank resulting in the homogenous mixing of effluents and helping in neutralization.
- Continuous mixing also eliminates settling of solids within the equalization tank.
- Reduces SS, TSS.
4. Flash mixer:- Coagulants are added to the effluents:
- Lime:(800-1000 ppm) To correct the pH upto8-9
- Alum: (200-300 ppm) To remove colour
- Poly electrolyte : ( 0.2 ppm) to settle the suspended matters and reduce SS, TSS.
5. Clarriflocculator:-
- In the clarriflocculator the water is circulated continuously by a stirrer.
- Flocculation provides slow mixing that leads to the formation of macro flocs, which then settles in the clarifier zone.
- Overflowing water goes out to the aeration tank.
- The solid particles settle down, and are collected separately; this reduces SS, TSS.
- The settled solids i.e. primary sludge is pumped into sludge drying beds.
6. Aeration Tank:-
- The effluent after clarification flows to an aeration tank for aerobic treatment.
- This tank is equipped with air blowers or diffusers using which air is passed through the tank.
- This air is required to maintain the desired dissolved oxygen (DO) level required for bacteria to grow and remove BOD and COD by breaking down the matter.
- BOD and COD values of effluent are reduced up to 90%.
7. Secondary Clarifier:-
- The overflow from aeration tank is led into the secondary clarifier where solid liquid separation takes place.
- The settled solids in secondary clarifier are called biological sludge, a part of which is recycled back into the aeration tank to maintain the desired MLSS level and remaining sludge is conveyed to sludge collection tank for further treatment.
- The outlet water quality is checked if it’s within the accepted.
- The treated water is disposed through pipelines.
8. Sludge Thickener:-
- The inlet sludge consists of 60% water + 40% solids.
- The effluent is passed through a centrifuge.
- Due to centrifugal action, the solids and liquids are separated.
- The sludge thickener reduces the water content in the effluent to 40% water + 60% solids.
- The effluent is then reprocessed and the sludge is collected at the bottom.
9. Drying Beds:-
- Primary and secondary sludge is dried on the drying beds to further reduce the water content.
Arvind Envisol is one of the best effluent treatment manufacturers in India and across the globe. In case of any queries feel free to reach us by filling the inquiry form on Contact Us page. We will get back to you within 24 hours.

SEWAGE TREATMENT PLANT (STP) MANUFACTURERS
Sewage is the waste generated from residential, institutional, commercial and industrial establishments. STP plant treats the sewage to make it fit for safe disposal, agricultural use or domestic use in toilets etc. Sewage usually contains a high quantity of organic and inorganic wastes. It is essential to treat sewage before it enters into any water body. If sewage, is allowed to enter the water sources without treatment, it will contaminate them; which is why it is essential to treat sewage properly before letting it into rivers or any other sources of water.
Areas in a STP Plant
Primary treatment
In Primary treatment, wastewater is fed to a screen to remove all large objects that are suspended in the water. After this, the water gets into a Grit chamber where the grit is removed. Grit includes sand, gravel, eggshells, bone chips, seeds and other materials. Grit removal is necessary to reduce heavy deposits in aeration tanks, digester, channels and conduits. The next step consists of primary settling tanks. These tanks are usually large in size and the solids settle down due to gravity and are removed as sludge from the bottom. Meanwhile, the oil floats on the surface and is skimmed off. 50-60% of the suspended solids get removed and a 30-40% reduction of the five-day biological oxygen demand can be expected.
Secondary treatment
Secondary treatment is the second stage of wastewater treatment. In primary treatment suspended solids, colloidal particles, oil and grease were removed. In secondary treatment biological treatment is done on the waste water to remove the organic matter present. This treatment is performed by indigenous and aquatic micro-organisms like bacteria and protozoa which consume biodegradable soluble contaminants like sugar, fat, detergent, food waste. These processes are sensitive to temperature and with increase in temperature rate of biological reactions increases. Secondary treatment is divided into two different treatment processes: 1. Aerobic treatment – Aerobic wastewater treatment is a biological treatment that uses oxygen to break down organic matter and remove other pollutants like nitrogen and phosphorus. Generally in the sewage treatment aerobic treatment is performed. 2. Anaerobic treatment – Anaerobic treatment is a process where wastewater or material is broken down by micro-organisms without the aid of dissolved oxygen. However, anaerobic bacteria can and will use oxygen that is found in the oxides introduced into the system or they can obtain it from organic material within the wastewater.
Tertiary treatment
Tertiary treatment is the third stage of the wastewater treatment and is also known as the advanced treatment. Tertiary treatment removes the load of nitrogen and phosphorus present in the water. It includes processes like filtration, ion exchange, activated carbon adsorption, electro dialysis, nitrification, and denitrification.Treatment options in tertiary treatment depend upon the characteristics of effluent after secondary treatment and what kind of water is needed at the end of the treatment. For example, if we need potable water then filtration and disinfection are to be done on the wastewater.Arvind Envisol is one of the best Sewage treatment plant manufacturers across the globe. In case of any queries feel free to reach us by filling the inquiry form on Contact Us page. We will get back to you within 24 hours
PACKAGED SEWAGE TREATMENT PLANT(PSTP)
Arvind Packaged Sewage Treatment Plant (PSTP) is housed in specially designed and highly durable FRP tank. These tanks are compact which can be utilized in decentralized manner at any location, either it’s underground or above the ground.
The Arvind Packaged STP is designed to bring the treated sewage parameters (BOD, COD, TSS, TN etc.) below the permissible limit which is stipulated by Pollution Control Board.MBBR technology is used in this system.

PROCESS DESCRIPTION OF ARVIND PACKAGE STP
1.Preliminary treatment
The influent sewage water passes through a bar screen to remove all the large objects like cans, rags, sticks, plastic packets etc. which are carried in the sewage stream.
2.Secondary treatment
a. Anaerobic Zone-
First stage of PSTP is oxygen depleted anaerobic zone in which the solids in raw sewage gets settled, while allowing the scum to float on the surface. It is a zone in which the settled sludge is stabilized by anaerobic digestion.
b. Anoxic Zone-
The sewage then enters the anoxic zone in which denitrification of the wastewater stream is accomplished by returning the activated sludge from the final sedimentation zone to the anoxic zone; where in dissolved oxygen levels are maintained approximate as 0.2 to 0.5 mg/l. In the denitrification process, anoxic microbes break down to the existing nitrates, this results in the release of inert nitrogen gas into the atmosphere.
c. Aeration Zone-
The sewage from solid separation zone flows into the aeration zone. Air is diffused with the help of air blowers which encourages the growth of bacteria cultures in and around the floating plastic media added in the aeration zone. The MBBR media provides the extended surface area for the growth of micro-organisms.
d. Sedimentation Zone-
The next step of treatment involves the sedimentation zone where organic waste is settled. The settled waste in the bottom of the tank is pumped back to the anoxic zone as a return sludge, which is done to ensure that quality of effluent must pass the stipulated sewage parameters.
3. Tertiary Treatment System:
The secondary treated sewage is then passed through the Pressure Sand Filter and Activated Carbon Filter for the removal of suspended solid (TSS), colour and odour. The treated water is then disinfected using sodium hypochlorite before it is reused.

1. INFLUENT
2. BAR SCREEN CHAMBER
3. ANAEROBIC & ANOXIC ZONE
4. AEROBIC MBBR ZONE
5. FINAL SEDIMENTATION
6. FILTER FEED TANK
7. MBBR MEDIA
8. AIR BLOWERS
9. RECIRCULATION PUMP
10. FILTER FEED PUMP
11. PRESSURE SAND FILTER
12. ACTIVATED CARBON FILTER
13. DISINFECTION
14. AIR VENT
15. TREATED WATER TANK
Key Points | Arvind MBBR FRP-PSTP |
---|---|
Performance | Decomposition of organic waste is consistent throughout the year. |
Monitoring of MLSS & F/M ratio | Required |
Sludge Removal | Once in 18-24 months. |
Chemicals & Equipment for Sludge Dewatering and Treatment | Required. |
Skilled Supervision | Not Required. |
O & M cost | 70% reduction compared to conventional STPs. |
Tank Maintenance | Leak & rust proof. No root integration & fungal growth. |
Tank Maintenance and Durability | Maintenance free and much more durable. |
Installation Lead Time | Within 7 to 10 days. |
Up-gradation and Relocation | Possible. |
SR. NO. | PRODUCTS |
---|---|
1 | FRP Package Sewage Treatment Plant (ENVI Model). |
2 | FRP Anaerobic Septic Tank (FAST Model). |
3 | FRP Waste Water Equalization / Collection Tank (FET Model). |
4 | FRP Water Storage Tank (FWST Model). |
5 | FRP Fire fighting Water Storage Tank (FFST Model). |
APPLICATION AND USES
- Residential and Commercial Complex
- Public Garden and National Park
- Hotel and Resort
- Restaurant
- Industry
- Institution
- Hospital
- Temple
- Government Office
- Labour Quarter
- Township
- Hostel
Zero Liquid Discharge (ZLD) India
Water is a scarce resource. Due to Urbanization and Globalization water usage will increase in the coming years. Industries like power, oil and gas, pharmaceuticals and chemicals generate large volume of wastewater which contains solid waste, organic waste, toxic and non-toxic chemicals which further affects the environment. In fact many government and industries have come up with initiatives to reduce water waste by installing ZLD, which in turn will reduce water wastage and help them attain a sustainable environment.
The key driver for zero liquid discharge is a growing concern about the impact of wastewater discharge on the environment. Such concern is resulting in increased regulation and limitation of waste water discharges. Organizations in India are targeting ZLD for their waste because they can sell the solids that are produced or reuse as a part of industrial process. For example, salt is the by-product we get at the last stage of ZLD. This salt can be used in textile process.
Zero liquid discharge is an advanced water treatment process which purifies and recycles the wastewater at the end of industrial process with zero liquid waste at end. Zero liquid discharge at Arvind Envisol is achieved in the most energy efficient method as it saves around 80% of the energy compared to the conventional ZLD techniques used by other companies. The reason why we are so efficient in this process is our patented polymeric film technology which we are using in Mechanical vapour recompression evaporator (MVRE).
Features of Arvind Envisol’s ZLD system are
- Saves up to 80% energy compared to other ZLD technologies.
- Approximate 95% of liquid can be recovered out of the liquid waste fed to the system for treatment.
- Treat and retrieve valuable by-products from your waste (i.e. salts and brines)
- Produce a dry, solid cake for disposal.

1.Mechanical Vapour Recompression Evaporator (MVRE)
MVRE is an energy recovery evaporator which compresses a low pressure vapour and produces a low volume of vapour with high pressure and temperature. In MVRE influent is heated with steam and the vapour produced are compressed and sent to a heat exchanger where it gets condensed and we get pure water at the outlet. Generally MVRE is used before MEE to reduce the TDS concentration of influent. This system is available in polymeric film technology. After RO effluent is fed into MVRE to remove high volatile compounds which were not removed in the previous process. In this process water recovered is approximately 80%.
MVRE is available in polymeric film technology.

2.Multi Effect Evaporator (MEE)
In MEE sequences of vessels are used. Here water is boiled in the vessels, each held at a lower pressure than the last, because the boiling temperature of the water decreases as pressure decreases the vapour boiled off in one vessel can be used to heat the next, and only the first vessel (at the highest pressure) requires an external source of heat. Effluent fed into MEE is of a kind which has very high TDS. Water recovery in this process is around 95%.